We live in a time when really sophisticated technology — wondrous stuff like a printer/scanner that can turn data into paper documents and paper documents into data — is so ubiquitous and cheap that it is practically disposable. A walk around any university campus will result in the finding of at least one such device lying in a dumpster. That was me today: walking around campus, I found an HP printer/scanner that was collecting dust, spider webs, and dried leaves. Well, I decided to take it apart.
Here’s what I saw when I took the cover off:
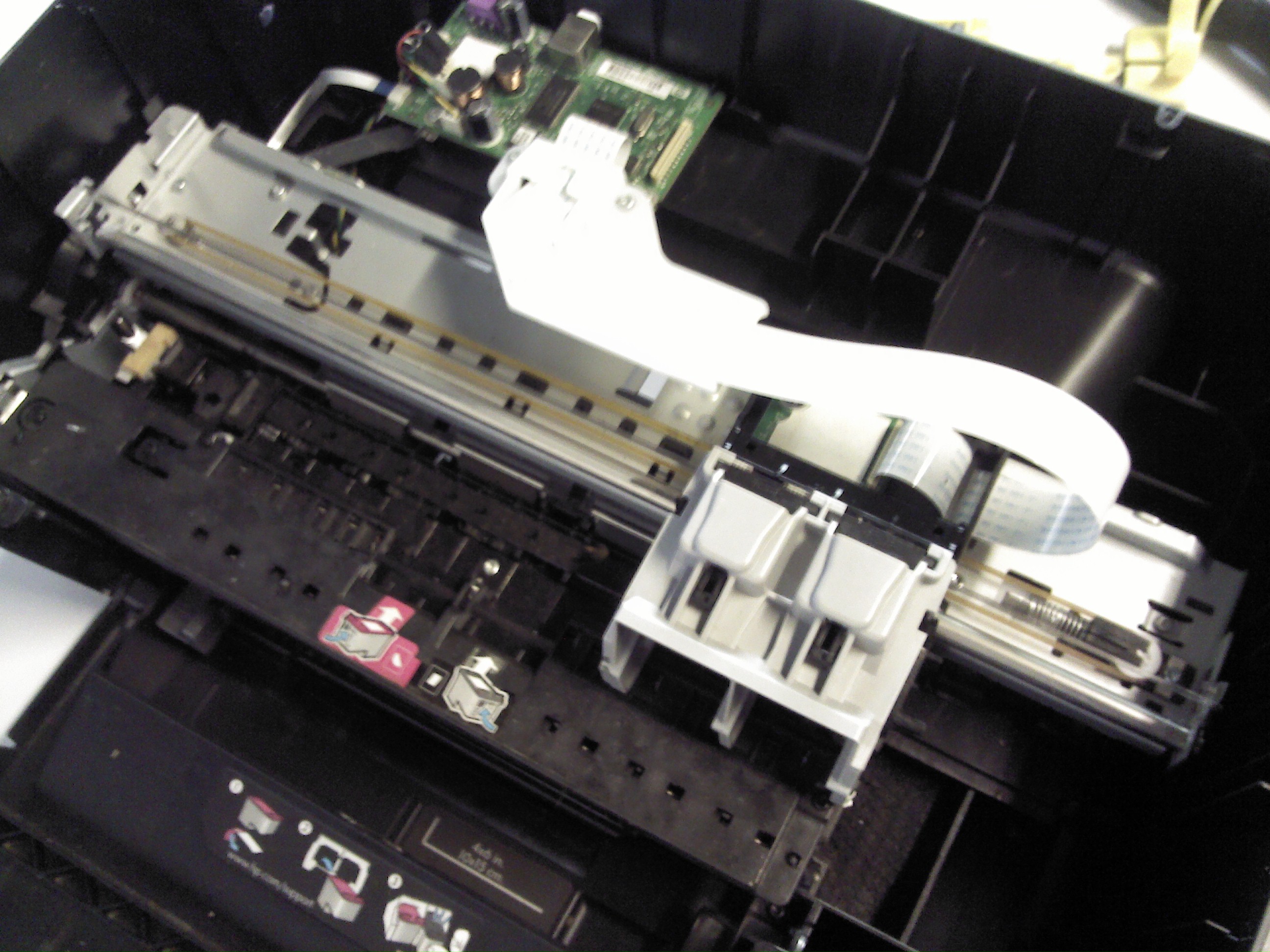
One of the coolest things inside were the linear and rotary encoders that provide position feedback. The main linear encoder measures the location of the cartridge carriage. It’s the clear plastic strip with a bunch of little lines on it:
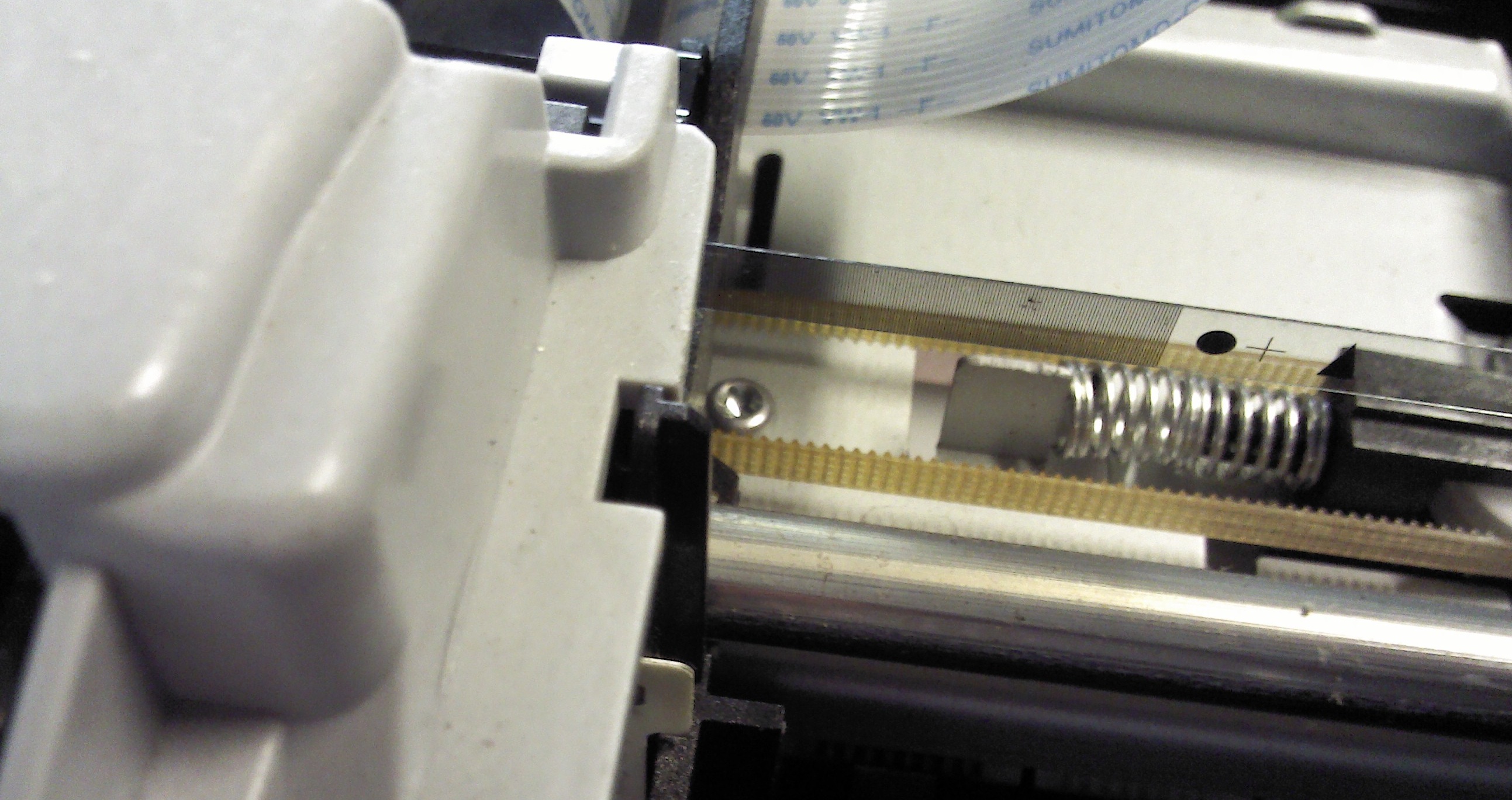
There’s an optical component on the carriage that can measure the passage of these lines, and by keeping count of how many lines have passed by, the printer knows exactly where the head is.
The fundamental accuracy of the printer depends on how closely these lines are spaced. I stuck the encoder under an optical microscope, and here’s what I saw:
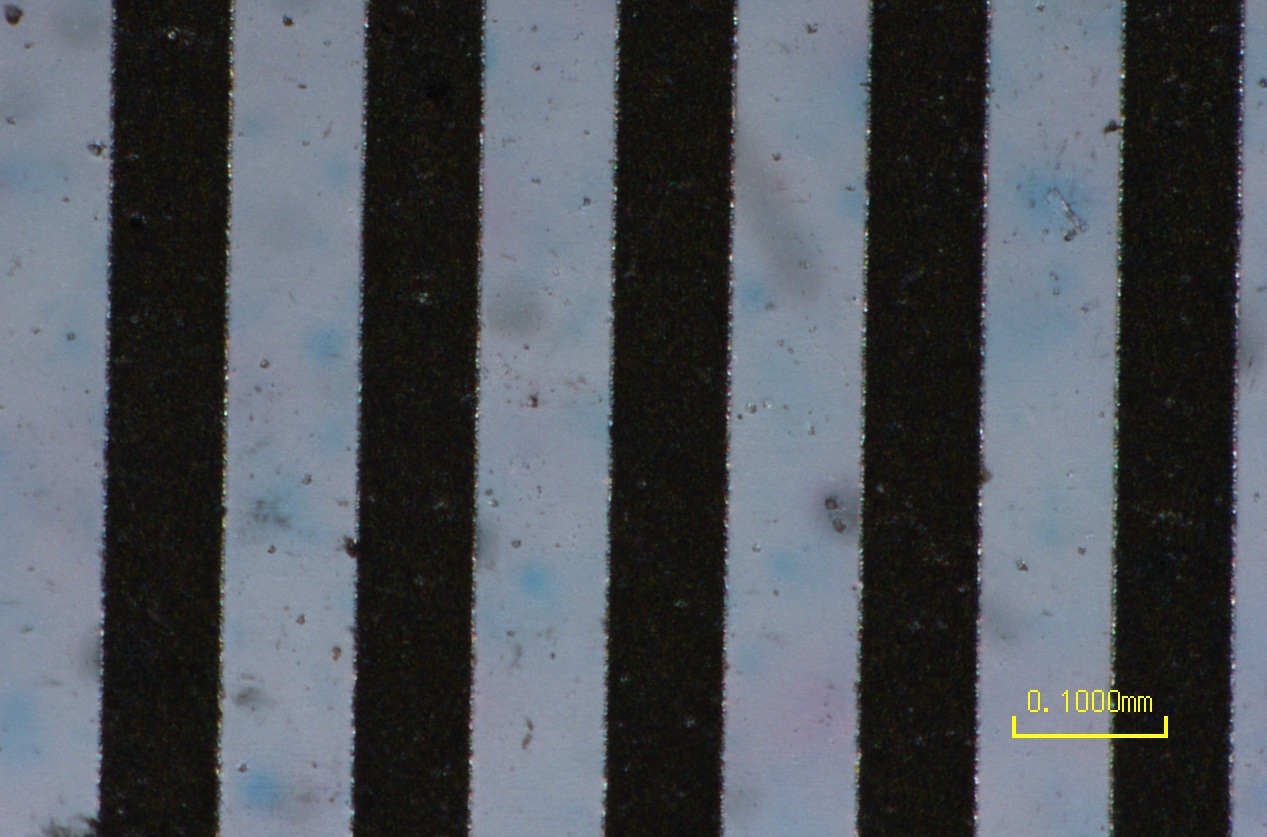
The lines are about 80 microns across, spaced 100 microns apart. This particular linear encoder was made by a company called pwb encoders.
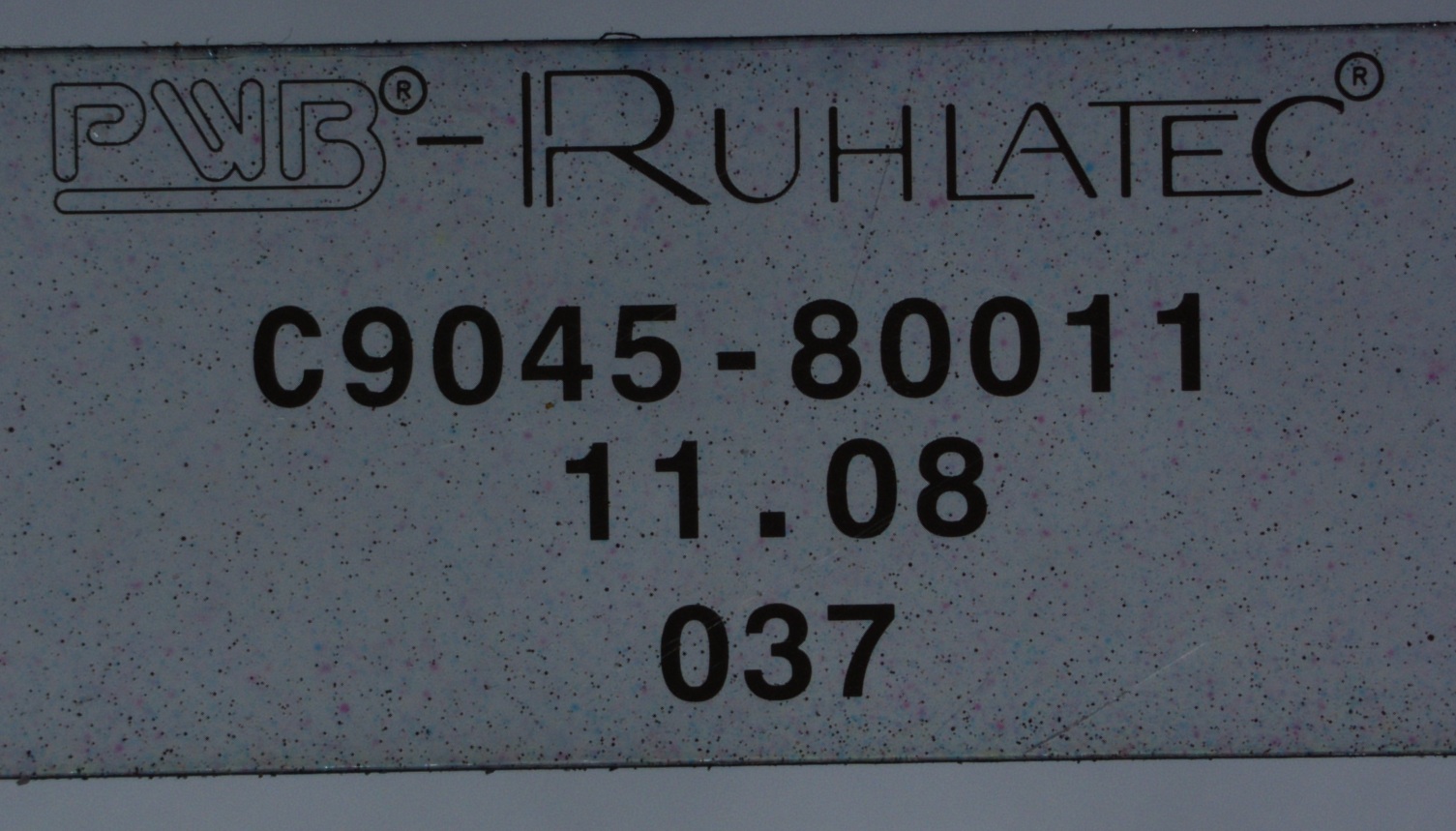
This particular printer also includes a rotary encoder made by pwb encoders.
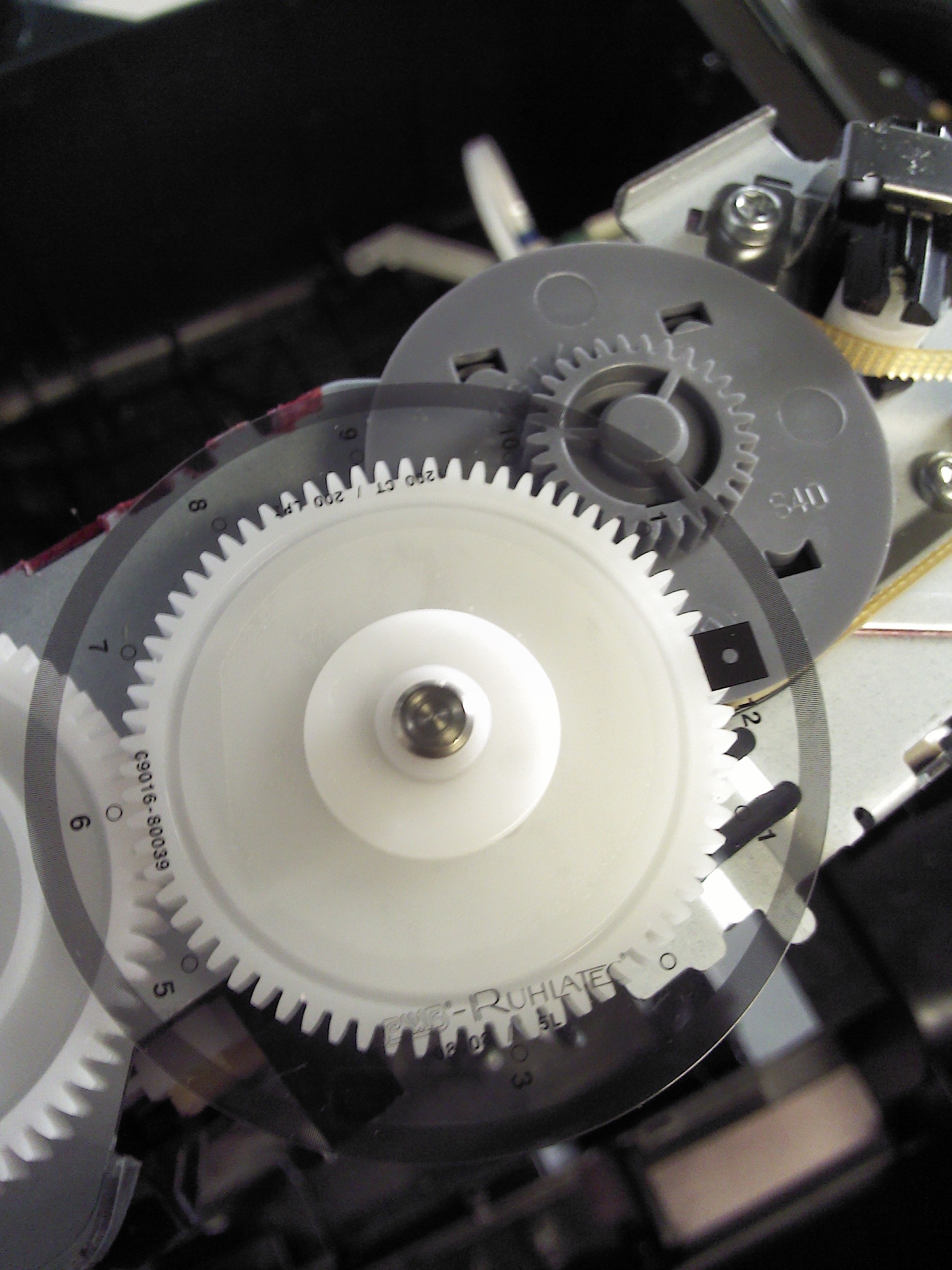
Another neat thing was the use of strip folding patterns to route ribbon cables. I did not know ribbon cables could be so creased, but there were some incredible 90- and 180-degree turns put on ribbon cables in this machine. Here’s one particularly gnarly example from the scanning head assembly:
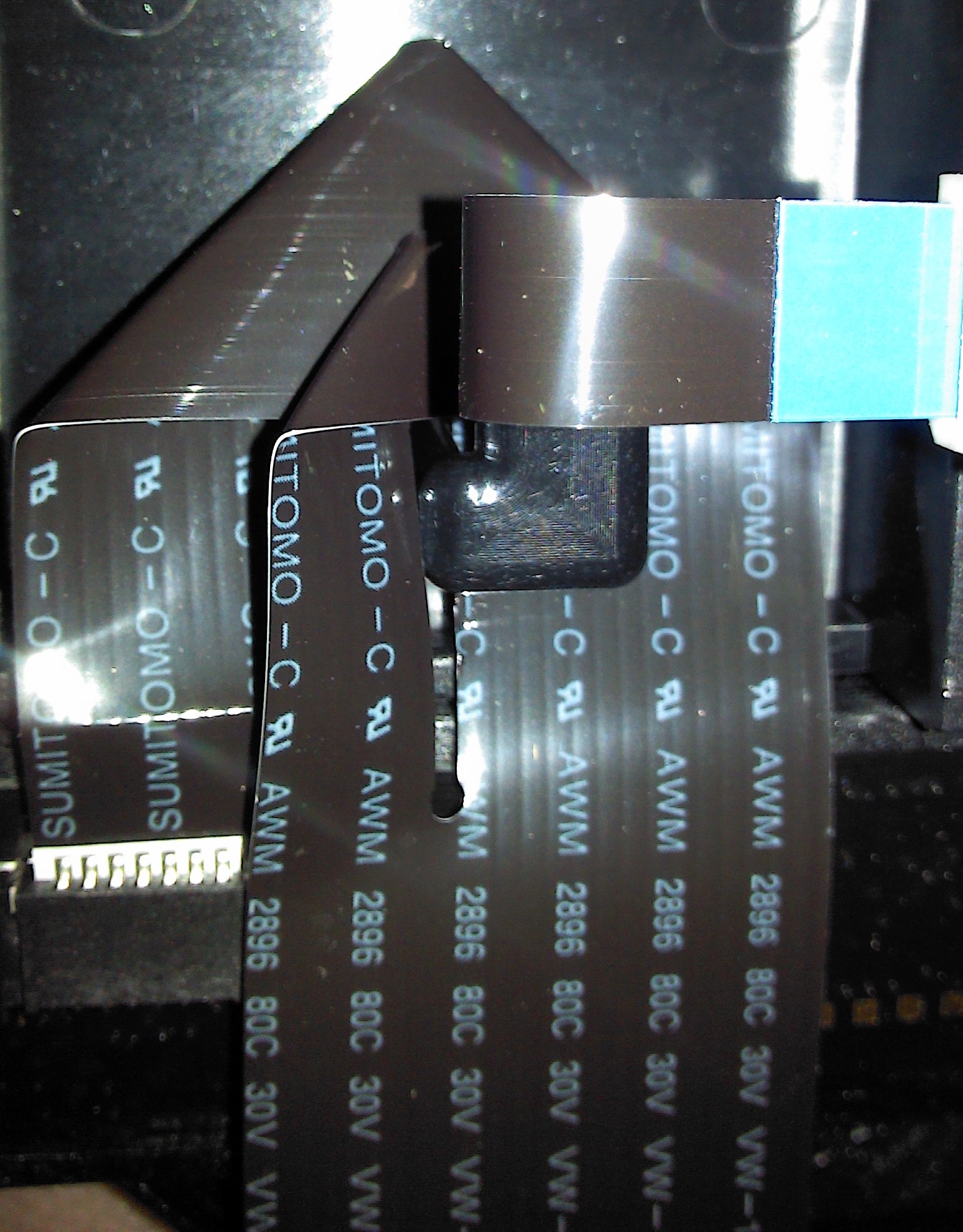
The last thing I want to talk about is the use of springs to set up kinematic mounts for certain components. The problem with overconstrained structures (and most structures are overconstrained) is that their exact shape is somewhat indeterminate from a purely kinematic perspective. Making a structure that constrains only the six rigid-body degrees of freedom without introducing a state of self-stress is tricky, but you need to do it whenever precise positioning is required.
For a printer, there are several components whose position you need to know down to tens of microns, or less. One particular example is the main rail on which the cartridge carriage rides. The way to (quasi-)kinematically mount this rail is to use a soft spring to constrain certain degrees of freedom. This spring is so soft that it can barely introduce a state of self-stress in the rail, but provides enough force to keep the rail in place.
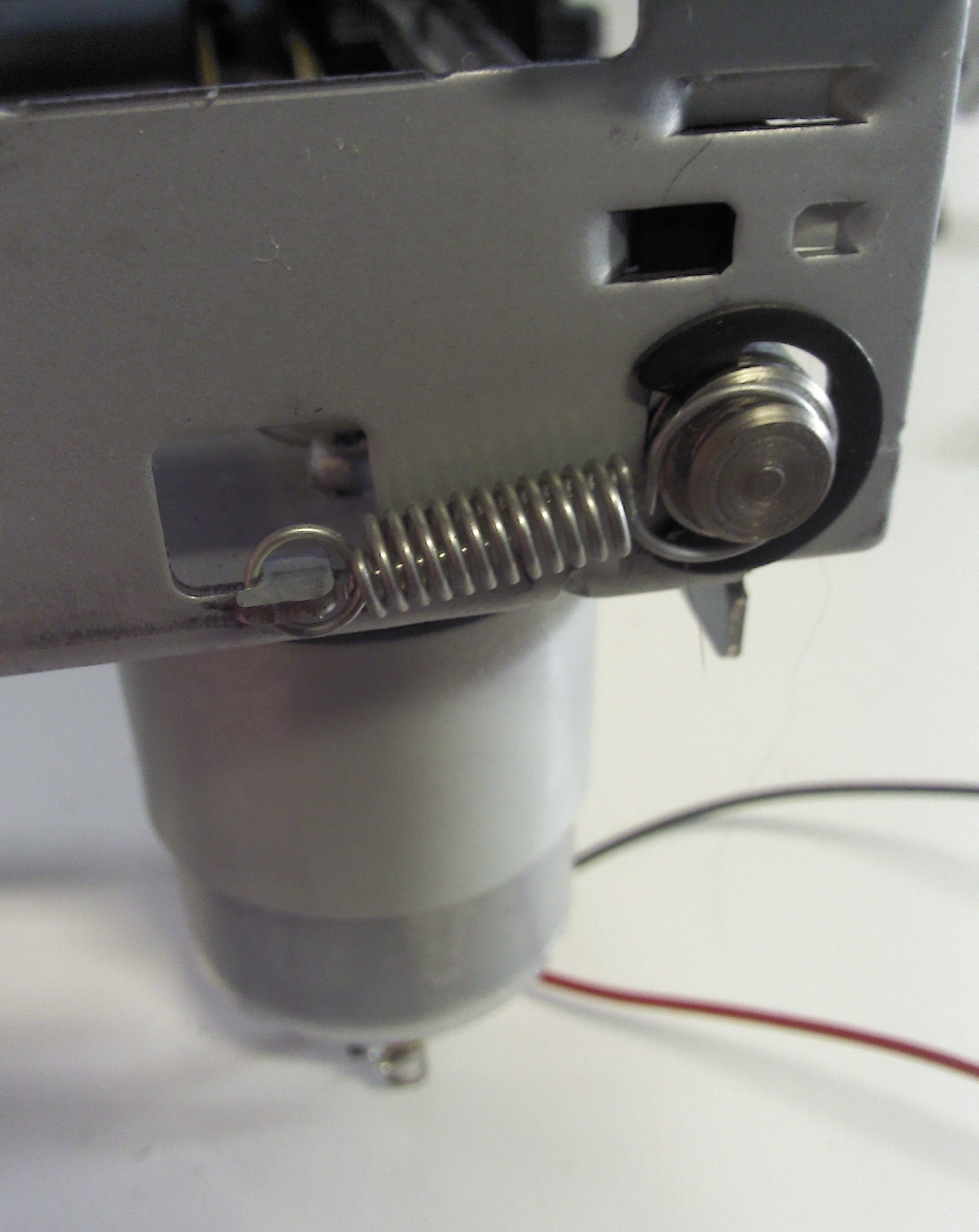
In all, I discovered six such sprung mounts for various components.
It was actually somewhat therapeutic, taking this thing apart, figuring out how it works. And, as a bonus, now I have a bunch of motors I can play with.
Comments
Commenting is closed for this article.